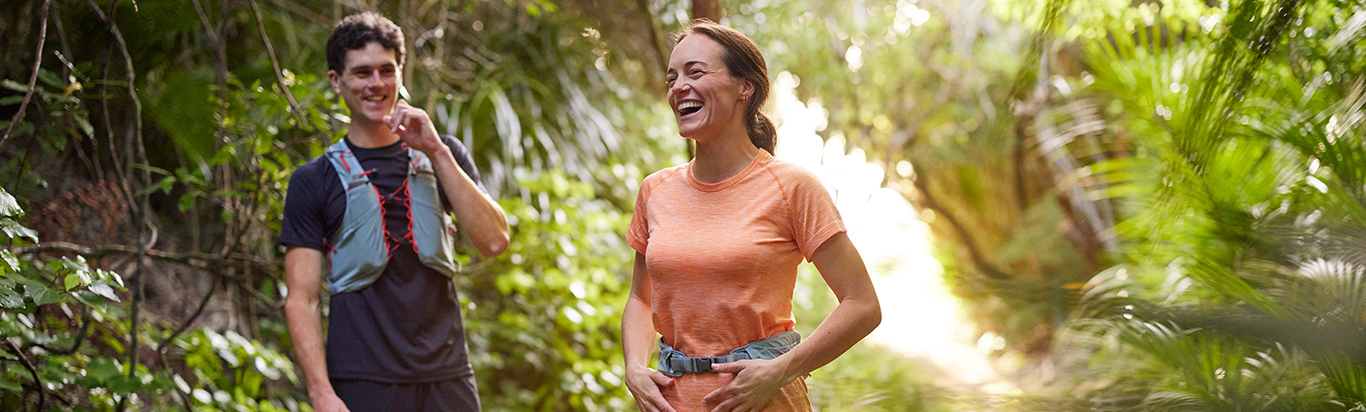
Our approach towards responsible packaging.
In the retail industry, packaging is a big thing. We’re constantly working to reduce the amount of packaging we use. The environmental impact of damaged apparel or gear is far worse than the environmental impact of recyclable packaging. Like other retailers, we use packaging to protect products during transport or storage, as well as to display critical product information to customers.
Our initial focus is to reduce the amount of recyclable plastic polybags we use in our supply chain. To do this, first we reviewed all our soft goods apparel products and how they were currently packaged.
Second, as down jackets are such a large percentage of our business, we asked all our Trade Partners who make product that comes pre-stuffed in stuff-sacs to just use one carton liner, rather than individual polybags, e.g. the Supernova down jacket.
Third, we set up packaging guidelines for all of our Macpac branded clothing and clothing accessories. These rules take into account things such as the product type, material, product value, retail display, transport and storage requirements.
Some products will still need their own packaging – due to the membranes or delicacy of the fabric, or the humidity at the manufacturer. Here are some examples:
- Clothing accessories such as gloves, socks and hats now have 10 – 20 products per polybag.
- Merino is more delicate, so merino clothing needs to be individually packaged.
Finally, we are working to identify the products with polybags that are too large and changing our order specs to include extra folding of the product to reduce the size of the polybags required.
We have also started ‘Direct to Store’ shipments. This means new product lines go straight from our manufacturing Trade Partner to our retail stores, rather than all to our Christchurch Distribution Centre. This has been set up for efficiency, less freight and handling but also to reduce polybags; now we can bundle more products into one polybag as they go straight into retail display.
Another focus is on reducing the amount of tissue paper used in our supply chain. Currently it is used over graphic prints on t-shirts to prevent the prints rubbing on the next shirt.
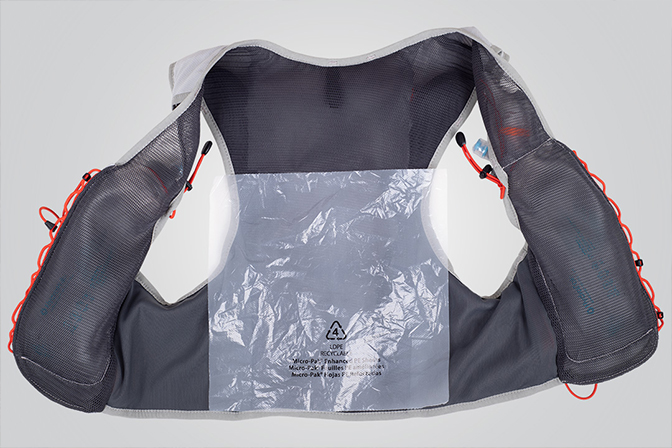
An example of Micro-Pak® PE Sheets that come with our packs
We are constantly working on finding better packaging solutions that are less harmful for the environment, while being reusable or easily recyclable. An example of this is our recent change from silica gel packs (commonly used to absorb moisture) to Micro-Pak® PE Sheets. While these sheets are made from plastic, they are recyclable (unlike the gel packs), far safer than the gel packs and more effective at eliminating mould, which means they protect our product better. These sheets now accompany each and every Macpac pack on their journey from our manufacturer to you.
While looking at packaging alternatives we still need to maintain our requirements for product protection, product information and retail display. This includes sourcing packaging made from certified post-consumer waste materials (our retail bags are made from 90% post-consumer waste) and paper products made from responsible sourced wood.
Currently, the blister packs used on some of our accessories pose a slight problem for us. We’re working on finding an alternative packaging solution for these products. In addition, we’re working on a restricted packaging materials list that our Trade Partners will need to adhere to, to avoid unwanted materials entering our supply chain.
Packaging improvements are an important part of our strategy. It is complex and will take time. We hope you stick with us on the journey.